Choosing the Right Container Filling Solution from WeighPack
Containers can come in all shapes and sizes…well, so do our machines!
More than likely, your business has devoted a lot of concerted effort and time into choosing the right containers.
After all, these packages say a lot about your company and convey your branding messages directly to the end consumers.
Have you invested in a food-safe, high quality rigid glass container or is your bulk product more conducive for a corrugated case or recyclable plastic tote?
In all circumstances, a lot of careful consideration goes into choosing the right automation solution to fill these packages.
When we collaborate with our clients, we ask all the appropriate questions upfront to ensure that we provide you with the best fit and all needs are met.
Top 3 things to consider when automating your container filling process:
1. Determine the size, shape and type of your containers
Getting accurate dimensions for the height of the container and the width of the container opening, along with the primary material are all very important factors in finding the right equipment for your business. The wider the container opening, the easier it is for filling machines like our Star Auger®, PrimoCombi®, and PrimoLinear™ to do their jobs.
For a business packaging tomatoes into a 10” wide plastic clamshell container, our staff may recommend a simple container indexing conveyor fed by our PrimoCombi® multi-head weigher. Container Indexing Conveyors easily fit in with existing packaging equipment and can accommodate low to mid output requirements.
If your business has a plastic tote or case that needs to accommodate a larger volume of product, we may recommend our PrimoLinear™ Series for bulk filling requirements. These systems have been commonly used for confections, frozen foods, hardware, produce and more.
Let’s say your business has a more challenging product that needs to be filled into a narrow mouth container… then, our SpinDexer® rotary container filling system with travelling funnels may be the way to go.
2. What are your accuracy and performance requirements?
How many containers are you currently filling per hour? Per day?
How many containers would you like to fill per hour? Per day?
Forecasting and planning for where your business will be in the coming months / years will allow you to make the best investment.
Our compact container indexing conveyor can handle entry level output requirements, while our high-performance SpinDexer® container filling system can fill up to 80 containers per minute.
3. What level of automation makes the most sense?
WeighPack manufactures solutions for all production requirements, budgets, and timeframes.
If your business is a small start-up with no existing automation, WeighPack can help.
If your business is a large corporation with high performance requirements, WeighPack can help.
For example, a start-up business may examine their numbers now and determine that it is most cost-effective to invest solely in a Container Indexing Conveyor System.
Our standard Container Indexing Conveyor System will require at least 2 operators. One operator will be loading empty containers onto the conveyor and the other will be unloading filled containers.
A year down the road, if the company has grown substantially and wants to take their automation a step further, we have a solution for that. WeighPack manufactures automatic unscrambling and accumulation tables that can be configured on each side of their existing conveyor. Adding these turning tables will allow the company to reallocate the operators to other important duties.
With WeighPack, there are no limits. Let us grow with you!
For more info on our variety of container filling solutions, give us a call at 1.833.4PAXIOM

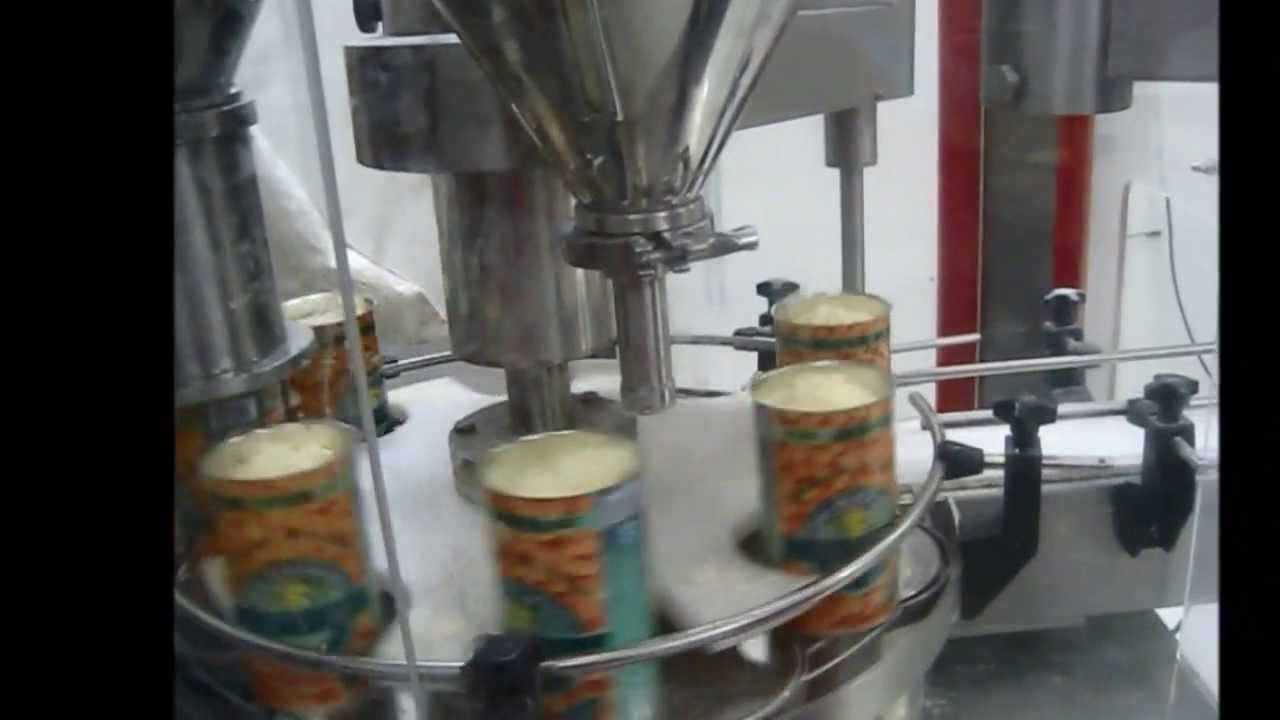